Determining Physical Properties of Ceramics
We have outlined our general procedure for determining the physical properties of ceramics, including apparent solid density, bulk density and apparent porosity. This structured approach ensures reliable and consistent data for material characterization and quality control purposes in accordance with ISO 18754 and ASTM C373 standards.
While we have provided a summary of our process here, it is essential to refer to the full standards for detailed guidance on preparing test specimens, conducting tests, and interpreting the results.
For both standards the boiling method was used for density and porosity measurements, our materials database incorporates these approaches to provide comprehensive data representation.
Specimen Preparation
For bulk density and porosity measurements the volume of each specimen was larger than 0.1 cm3 with a mass exceeding 50g in conformance to both ISO 18754 and ASTM C373. Specimens were typically cylindrical and were prepared using precise machining or molding techniques to ensure smooth surfaces free from defects such as notches, glazes or significant voids.
Specimen testing and conditioning were conducted at room temperature, defined as 23°C ± 5°C (73.4°F ± 9°F), and relative humidity of 50% ± 10%, ensuring stable environmental conditions during measurements.
Apparatus
For mass measurements a precision balance was utilized, specimens were prepared in a drying oven and boiled in a water immersion tank fitted with setting pins to ensure full immersion.
Procedure
The dried mass of specimens was obtained by heating in a drying oven for a specified temperature and time followed by weighing.
- For ISO 18754 testing specimens were dried at 110°C ± 5°C (230°F ± 9°F) then allowed to cooling to room temperature in a dessicator.
- For ASTM C373 testing specimens were dried at 150°C (302°F) then allowed to cooling to room temperature in a dessicator.
The apparent mass of the immersed specimens was obtained by boiling in distilled water (ensuring full immersion) for a specified temperature and time, and then weighing while maintaining immersion. The soaked mass was also taken by removing the specimen from the liquid and removing any excess water.
- For ISO 18754 testing specimens were boiled for 3hrs and then allowed to cool to room temperature in water.
- For ASTM C373 testing specimens were boiled for 5hrs and then allowed to soak for an additional 24hrs.
Test Outcomes
As per the equations laid out in ISO 18754 and ASTM C373 the apparent solid density, bulk modulus and apparent porosity could be determined.
For the listed material properties in the Manta Materials data tables, the values are averaged from multiple test specimens per standard, with adjustments made for testing tolerances and uncertainties.
Flexural Testing of Ceramics
We have outlined our general procedure for flexural testing of advanced ceramics. This structured approach ensures reliable and consistent data for material characterization and quality control purposes in accordance with ISO 14704 and ASTM C1161 standards.
While we have provided a summary of our process here, it is essential to refer to the full standards for detailed guidance on preparing test specimens, conducting tensile tests, and interpreting the results.
Both standards aim to determine similar properties but differ in aspects such as specimen dimensions, testing speeds, and the calculation of flexural properties. Our materials database incorporates both approaches to provide comprehensive data representation.
Specimen Preparation
All test specimens were prepared using precise machining or molding techniques to ensure smooth surfaces free from defects such as notches, voids, or surface roughness that could affect the tensile properties.
- ISO 14704: Specifies the use of rectangular bars with a length-to-thickness ratio of at least 4:1 and smooth surfaces to minimize stress concentrations. The standard also allows for the use of round specimens with specified dimensions.
- ASTM C1161: Recommends using rectangular specimens with defined dimensions, typically 3 mm x 4 mm x 45 mm for standard tests, with a length-to-thickness ratio of 10:1 to ensure uniform stress distribution.
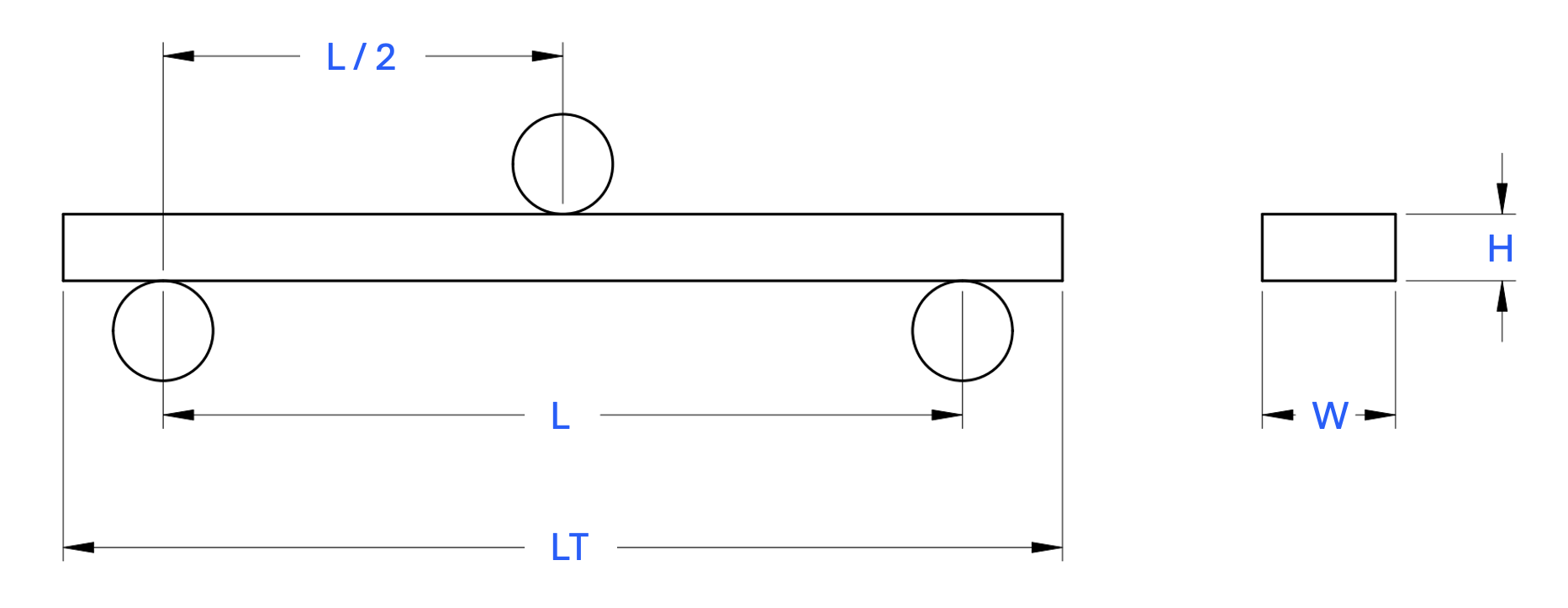
# | Dimensions | ISO 14704 | ASTM C1161 Configuration B |
---|---|---|---|
L | Support Span | 40 | 40 |
L | Length of Narrow Section | 25 | |
WO | Width overall (minimum) | 16 | |
LO | Length overall (minimum) | 80 | |
R | Radius | 6 | |
G | Gauge Length | 20 | |
D | Distance between grips | 64 | |
T | Thickness | 3 |
Specimen testing and conditioning were conducted at room temperature, defined as 23°C ± 5°C (73.4°F ± 9°F).
Apparatus
All testing was conducted using a universal testing machine equipped with suitable grips and calibrated force measurement systems in accordance with ISO 7500-1 and ASTM E4. The grips were designed to prevent slippage without introducing additional stress to the specimen, ensuring accurate load application.
An extensometer was used to measure the strain, particularly in the elastic region, and was calibrated in accordance with ISO 9513 or ASTM E83 standards, depending on the test method used.
Procedure
The following test procedure was used for tensile testing of ceramics according to each standard:
- Specimen Preparation: Each specimen was prepared to meet the specified dimensions and surface quality requirements. Specimens were cut or molded according to standard specifications to ensure uniformity.
- Conditioning: The specimens were conditioned at 23°C ± 5°C (73.4°F ± 9°F) and 50% relative humidity for at least 16 hours to reach equilibrium with the testing environment, as recommended by both standards.
- Specimen Mounting: The specimen was placed in the grips of the testing machine, ensuring proper alignment to prevent bending or off-axis loading. The grip pressure was carefully adjusted to avoid specimen damage.
- Applying Load: A tensile load was applied at a constant crosshead speed, typically 0.5 mm/min or as specified in the standard. The load was increased until the specimen reached yield or fractured.
- Data Collection: The force and corresponding strain data were recorded continuously to capture the stress-strain behavior of the material, including the modulus of elasticity, yield strength, tensile strength, and elongation at break.
Test Outcomes
The following mechanical properties are calculated from the tensile test data for ceramics:
- Tensile Strength: The maximum stress that a material can withstand while being stretched or pulled before breaking, calculated from the peak load applied during the test divided by the original cross-sectional area of the specimen.
- Modulus of Elasticity: The ratio of stress to strain in the elastic deformation region of the stress-strain curve, indicating the material's stiffness.
- Elongation at Break: The increase in gauge length measured after fracture, expressed as a percentage of the original gauge length, indicating the ductility of the material.
- Fracture Toughness: The ability of a material containing a crack to resist fracture, an important property for ceramics due to their brittle nature.
For the listed material properties in the Manta Materials data tables, the values are averaged from multiple test specimens per standard, with adjustments made for testing tolerances and uncertainties.
Rockwell Hardness Testing of Rigid Plastics
We have outlined our general procedure for Rockwell hardness testing of rigid plastics at room temperature. This structured approach ensures reliable and consistent data for material characterization and quality control purposes in accordance with ISO 2039-2 and ASTM D785 standards.
While we have provided a summary of our process here, it is essential to refer to the full standards for detailed guidance on preparing test specimens, conducting hardness tests, and interpreting the results.
Both standards aim to determine the hardness of rigid plastics, but they differ in aspects such as indenter types, loads applied, and testing procedures. Our materials database incorporates both approaches to provide comprehensive data representation.
Specimen Preparation
All test specimens were prepared using precise machining techniques to ensure flat, smooth surfaces that are free from defects such as notches, scratches, or indentations that could affect the hardness measurements.
- ISO 2039-2: Specifies the use of flat specimens with a minimum thickness of 6 mm to ensure that the material's hardness is accurately measured without influence from the substrate. The specimen surface must be flat and free from damage to ensure proper contact with the indenter.
- ASTM D785: Recommends using flat specimens with a thickness of at least 3.2 mm (0.125 in.). The surface should be smooth and free from imperfections, ensuring consistent hardness measurements across multiple test points.
# | Specimen Requirements | ISO 2039-2 | ASTM D785 |
---|---|---|---|
1 | Minimum Thickness | 6 mm | 3.2 mm (0.125 in.) |
2 | Surface Condition | Flat and free from damage | Flat and smooth |
3 | Number of Indentations | 3 or more, depending on specimen size | 3 or more, evenly spaced |
Specimen testing and conditioning were conducted at room temperature, defined as 23°C ± 5°C (73.4°F ± 9°F).
Apparatus
All testing was conducted using a Rockwell hardness tester equipped with a suitable indenter and load application system. The testing apparatus was calibrated in accordance with ISO 2039-2 and ASTM D785 standards to ensure accurate hardness measurements.
The indenter used was a steel ball (1/8 inch or 3.18 mm in diameter), and the load applied was consistent with the specific Rockwell scale (Rockwell M, L, R) designated for rigid plastics. The test apparatus was equipped with a digital readout to record the hardness value accurately.
Procedure
The following test procedure was used for Rockwell hardness testing of rigid plastics according to each standard:
- Specimen Preparation: Each specimen was prepared to meet the specified thickness and surface condition requirements. Specimens were cut or machined to provide a flat testing surface free of any surface imperfections.
- Conditioning: The specimens were conditioned at 23°C ± 5°C (73.4°F ± 9°F) and 50% relative humidity for at least 16 hours to reach equilibrium with the testing environment, as recommended by both standards.
- Specimen Placement: The specimen was placed on the anvil of the Rockwell hardness tester. The surface to be tested was positioned directly under the indenter to ensure proper alignment and contact.
- Applying Load: A preliminary minor load was applied to seat the indenter, followed by the major load required for the specific Rockwell scale being used. The indenter was held in place for a specified dwell time to allow for any viscoelastic recovery.
- Data Collection: The Rockwell hardness number (HR) was automatically calculated and displayed on the machine's digital readout. Multiple readings were taken at different points on the specimen to ensure consistency and repeatability of results.
Test Outcomes
The following properties are determined from the Rockwell hardness test data for rigid plastics:
- Rockwell Hardness Number (HR): The depth of penetration of the indenter under a specified load, expressed in terms of the Rockwell hardness scale (M, L, or R). Higher numbers indicate harder materials.
- Consistency Across Multiple Indentations: The uniformity of hardness measurements across different points on the specimen surface provides insight into the material's homogeneity and surface condition.
For the listed material properties in the Manta Materials data tables, the values are averaged from multiple test specimens per standard, with adjustments made for testing tolerances and uncertainties.
Apparatus
Rockwell hardness tester fitted with a flat anvil of at least 50mm. The indentor sizes used were 1/8in (3.18mm) / 1/4in (6.35mm) / ½ in (12.7mm) balls
Methodology
The surface conditions were as machined, ensuring measurement faces were free of bulges, markings, or defects. Rockwell hardness scales R / L / M / E were made at the following conditions:
Rockwell Hardness Scale | Minor Load (N) | Major Load (N) | Indentor Diameter (mm) |
---|---|---|---|
R | 10 | 60 | 12.7 |
L | 10 | 60 | 6.35 |
M | 10 | 100 | 6.35 |
E | 10 | 100 | 3.175 |
Tests were carried out in accordance with ISO 2309-2 and ASTM D785. In each case, at least five hardness tests were made, and for anisotropic materials, five tests were made along each principal axis of anisotropy.
Specimens
Test specimens have a thickness exceeding 6mm, with flat parallel surfaces, and were typically circular cross-section with diameters exceeding 25mm.
Electrical Conductivity Testing of Rigid Plastics
We have outlined our general procedure for electrical conductivity testing of rigid plastics at room temperature. This structured approach ensures reliable and consistent data for material characterization and quality control purposes in accordance with ISO 3915 and ASTM D257 standards.
While we have provided a summary of our process here, it is essential to refer to the full standards for detailed guidance on preparing test specimens, conducting electrical conductivity tests, and interpreting the results.
Both standards aim to determine the electrical conductivity of rigid plastics but differ in aspects such as specimen dimensions, test methods, and calculation of electrical properties. Our materials database incorporates both approaches to provide comprehensive data representation.
Specimen Preparation
All test specimens were prepared using precise machining techniques to ensure they meet the required dimensions and surface conditions. Specimens were made flat, smooth, and free from defects such as voids or surface irregularities that could affect the electrical conductivity measurements.
- ISO 3915: Specifies using flat specimens with a minimum thickness of 1 mm and a sufficient size to ensure proper contact with electrodes. The surface should be smooth to ensure uniform electrical contact.
- ASTM D257: Recommends using flat, rectangular specimens with a minimum thickness of 1 mm and dimensions large enough to accommodate the electrodes. The surface must be free of contaminants and polished to ensure good electrical contact.

# | Specimen Requirements | ISO 3915 | ASTM D257 |
---|---|---|---|
1 | Minimum Thickness | 1 mm | 1 mm |
2 | Specimen Size | Sufficient to ensure proper electrode contact | Large enough to accommodate electrodes |
3 | Surface Condition | Smooth and free from defects | Polished and free of contaminants |
Specimen testing and conditioning were conducted at room temperature, defined as 23°C ± 5°C (73.4°F ± 9°F).
Apparatus
All testing was conducted using a resistivity meter or electrometer capable of measuring low conductivity materials, equipped with electrodes suitable for rigid plastics. The testing apparatus was calibrated in accordance with ISO 3915 and ASTM D257 standards to ensure accurate measurements of electrical conductivity.
The apparatus was equipped with a high-impedance voltage source and sensitive current measuring device to detect small currents passing through the specimen, ensuring precise determination of electrical conductivity.
Procedure
The following test procedure was used for electrical conductivity testing of rigid plastics according to each standard:
- Specimen Preparation: Each specimen was prepared to meet the specified dimensions and surface condition requirements. Specimens were cut or machined to provide a flat testing surface free of any surface imperfections or contaminants.
- Conditioning: The specimens were conditioned at 23°C ± 5°C (73.4°F ± 9°F) and 50% relative humidity for at least 16 hours to reach equilibrium with the testing environment, as recommended by both standards.
- Specimen Placement: The specimen was placed between the electrodes of the resistivity meter, ensuring proper alignment and contact to avoid any gaps that could affect the measurements.
- Applying Voltage: A specified voltage was applied across the specimen while the current passing through it was measured. The voltage and current were monitored to ensure they remained within the limits specified by the standards.
- Data Collection: The electrical conductivity (σ) was calculated based on the measured current, applied voltage, and specimen dimensions. Multiple measurements were taken to ensure consistency and repeatability of results.
Test Outcomes
The following electrical properties are determined from the electrical conductivity test data for rigid plastics:
- Electrical Conductivity (σ): The ability of a material to conduct electric current, calculated based on the measured current, applied voltage, and specimen dimensions. It is expressed in siemens per meter (S/m).
- Volume Resistivity (ρ): The measure of a material's resistance to electric current flow through its volume, inversely related to electrical conductivity. It is expressed in ohm-meters (Ω·m).
For the listed material properties in the Manta Materials data tables, the values are averaged from multiple test specimens per standard, with adjustments made for testing tolerances and uncertainties.